

Thus the confusion - people would say “MMC” when discussing the datum, but had to understand that it wasn’t really the true MMC that would be simulated.
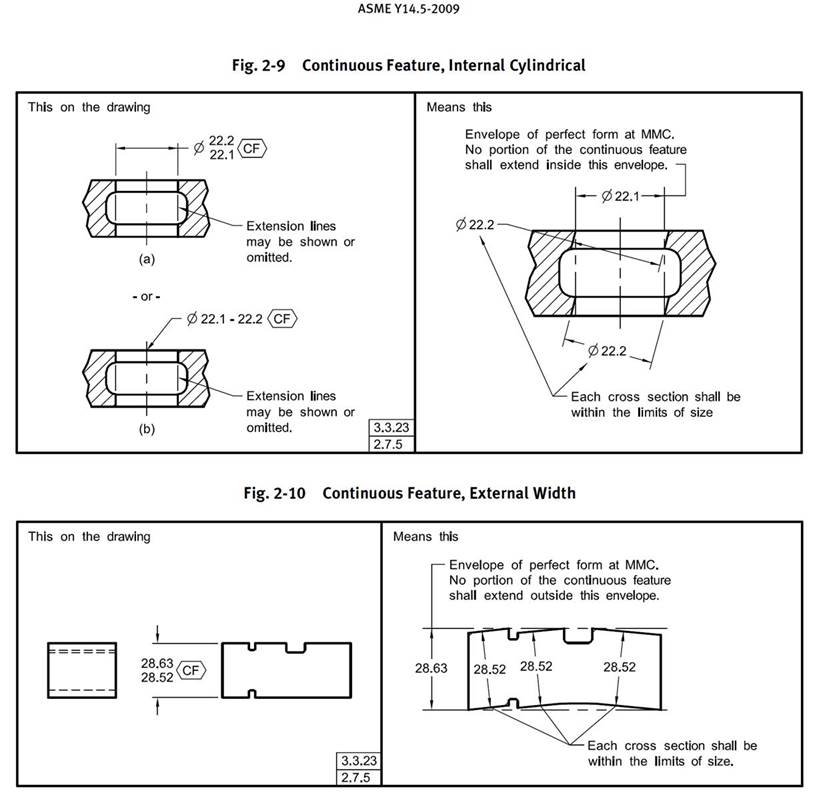
It would not really be simulating the MMC of 22.0 instead, it would be 21.8 in order to accommodate the perpendicularity tolerance of 0.2. But here’s the key: think about the size of a gage pin that would be inserted into the center hole (it should be attached to a flat plate that simulates datum A). The position tolerance references datum feature B with the M symbol. The reason this was introduced was to eliminate confusion when the M symbol is modifying a datum that has its own geometric tolerance. Yet it is invoked using the same circled M symbol. Well, a new item for the 2009 standard is something very similar, called “maximum material boundary,” or MMB.

This concept is invoked when the circled M symbol is placed in a feature control frame. The term “maximum material condition” or MMC has been around for a long time. In today’s column, I’d like to introduce you to one of the changes. If you are a regular user of GD&T, you probably know that the ASME standard was recently revised (for details, see the blog entry below dated March 28, 2009).
